Running an efficient beer, wine and spirits warehouse operation
Share
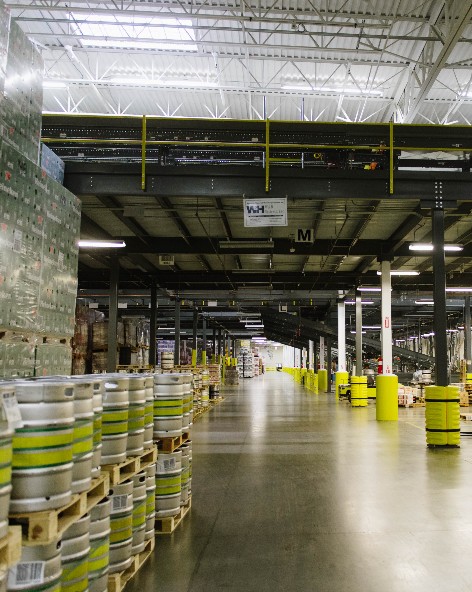
Share
Running an efficient beer, wine and spirits warehouse operation is an elaborately collaborative effort. There are many key internal and external customers that must work together, brainstorm, and pass information along in a timely manner in order to ship accurately and efficiently. The sales divisions, customer service reps, IT department, day crew, night crew, drivers, and driver helpers all play a vital role in getting your favorite frosty beverage to your local bar in time for #ThirstyThursday.
It all starts with the sales division. Sales men and women will go out in the trade promoting products, checking retail inventory levels, and taking orders from their accounts. A slip of the finger when inputting item numbers can send an account a case of Korbel Blanc De Noir (SKU 8432) instead of the Jack Daniel’s liters (SKU 8243) they were hoping for. “Korbel and Coke” doesn’t have quite the same ring to it and certainly not the same taste. Customer service reps could make this same mistake. Furthermore, they are often expected to figure out which item a customer wants based on vague descriptions, which can sometimes lead to similar issues. When a busy bar manager is on the phone shouting over the crowd that he needs “ten cases of that new fruity beer,” does he mean the Harpoon Wannamango that is the latest craze, or Stony Creek Sun Juice, a lesser known, albeit just as delicious, new craft beer launching in the South Shore?
Since Horizon moved to an automated warehouse management system in April 2012 the IT department has become even more vital to warehouse operations than ever before. If the UPCs on the cases aren’t scanned and updated correctly, then a pallet of delicious Jim Beam Apple could be scanned in under the SKU for Jacob’s Ghost, a white whiskey without the flavor of apple. The slightest breakdown in technology, if not fixed quickly or maintained properly, can shut down the entire operation, leading to liquor outages across the state, which would quickly turn Massachusetts into an episode from the last season of The Walking Dead.
All of these departments help to run an efficient warehouse, and none of them actually work IN the warehouse. The day crew still has to receive the product properly, replenish it to the high volume pick modules efficiently, and fix any inventory issues along the way. The night crew still has to pick the correct product, load it safely on to the trucks, and make sure the invoices print accurately for the drivers. Finally, the drivers still have to drive safely, get to the stop on time, and along with the driver helper, unload the correct cases.
All of these teams work hard and work together to make sure that our customers have the right product for their customers to drink at the restaurant, bar or pull from the liquor store shelves to enjoy in the comfort of home. Teamwork truly does make the dream work, especially when the dream is a delicious alcoholic beverage of your choice!